Fixtures are specialized tools designed to securely hold, position, and interface with components during testing, assembly, or calibration processes. At Petra Carbon, we engineer high-precision fixtures for industries ranging from electronics manufacturing to aerospace, ensuring repeatability, accuracy, and efficiency. This guide explores the role of fixtures in modern production, their applications, and how Petra Carbon’s solutions optimize quality control.
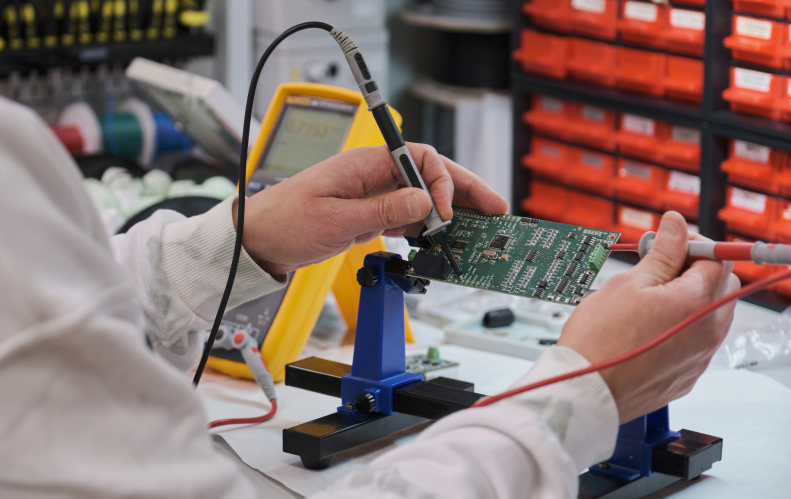
What Is a Fixture?
A fixture is a custom-designed device that holds a workpiece or component in a fixed position, enabling consistent testing, machining, or assembly. Unlike jigs (which guide tools), fixtures focus on stability and repeatability, critical for high-volume production or sensitive PCB testing.
Key Features of Petra Carbon’s Fixtures:
- Material Durability: Aluminum, stainless steel, or engineering plastics for longevity.
- Modular Design: Interchangeable components for multi-product compatibility.
- Integration: Compatible with Teradyne in-circuit test systems and Keysight instrumentation.
Explore our testing equipment catalog for fixture-ready solutions.
Types of Fixtures
PCB Test Fixtures
Use Case: Validating printed circuit boards (PCBs) for defects like open circuits or shorts.
Features: Spring-loaded probes, vacuum sealing for secure PCB clamping.
Pair With: Board test probes for electrical continuity checks.
RF Test Fixtures
Use Case: Calibrating antennas, RF connectors, or coaxial cables.
Features: EMI-shielded enclosures, SMA/N-type terminations.
Industrial Assembly Fixtures
Use Case: Aligning components during hydraulic tool assembly or calibration.
Features: Adjustable clamps, laser-etched alignment markers.
Applications of Fixtures
Electronics Manufacturing
PCB Testing: Detect faults in high-speed digital or RF circuits.
Sensor Calibration: Ensure accuracy in IoT device production.
Aerospace & Defense
Avionics Testing: Secure delicate components during vibration/shock tests.
Automotive
ECU Validation: Test engine control units under simulated operating conditions.
Industrial Automation
Hydraulic Tool Assembly: Align components for hydraulic torque wrenches with micron-level precision.
How to Design an Effective Fixture
Step 1: Define Requirements
Workpiece Size: Match fixture dimensions to components (e.g., PCBs, connectors).
Testing Needs: Electrical, mechanical, or environmental (thermal/vibration).
Step 2: Select Materials
Metals: For high-stress environments (e.g., aerospace).
Plastics: Lightweight, cost-effective for consumer electronics.
Step 3: Integrate Probes/Sensors
Use coaxial probes for RF testing or strain gauges for mechanical stress analysis.
For custom designs, contact our engineering team.
Why Petra Carbon’s Panel Antennas Excel
Precision Engineering: Fixtures are validated using in-circuit test systems for accuracy.
Rapid Prototyping: 3D-printed models available for design verification.
Scalability: Solutions for low-volume R&D or high-volume production.
FAQs About Fixtures
How often should fixtures be recalibrated?
Annually for most applications, or after 10,000 cycles in high-volume production.
Can fixtures be modified for new products?
Yes! Modular designs allow component swaps for new form factors.
What’s the lead time for a custom fixture?
Typically 2–4 weeks, depending on complexity.
At Petra Carbon, we deliver fixtures engineered for reliability, whether you’re testing PCBs or assembling industrial tools.
🔗 Contact Us for custom solutions or explore our Testing Equipment Hub.
Reliable fixtures, proven performance!