Flange Facers are essential tools in industrial sectors where equipment reliability, worker safety, and leak prevention are non-negotiable. The surface condition of flange joints plays a critical role in maintaining system integrity. Whether you’re dealing with aging pipeline systems offshore or corrosion-prone heat exchangers in a petrochemical plant, a damaged flange face can compromise sealing integrity and increase the risk of catastrophic failure. That’s where high-precision flange facers come in.
At Petracarbon we’ve worked alongside industries for decades to deliver portable flange facing tools capable of restoring sealing surfaces to industry standards-right on site. Whether in emergency shutdowns, scheduled plant maintenance, or remote offshore repairs, our solutions are built for accuracy, dependability, and mobility.
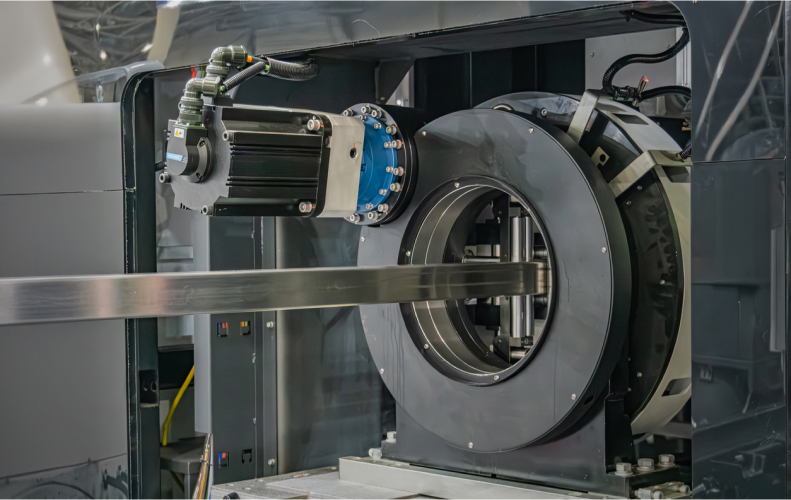
Why Precision Refacing Matters for Safety and Reliability
- Leak Prevention: Damaged or uneven flange faces cause gasket misalignment, resulting in persistent leaks under high pressure.
- Operational Continuity: Refacing eliminates the need to replace entire flanges or pipe sections, minimizing downtime.
- Compliance: Facing tools help meet ASME B16.5, EN 1092-1, and other international surface finish standards for flange joints. Contact Pins Fixture 3070 Teradyne
Types of Flange Facers and Their Application Environments
Manual vs. Powered Flange Facers
Manual flange facers are preferred for small-diameter flanges and areas with restricted access. They’re lightweight, easy to carry, and ideal for quick maintenance tasks. On the other hand, powered flange facers-available in pneumatic or hydraulic configurations-handle larger diameters, tougher materials, and longer cuts without operator fatigue.
Type | Power Source | Ideal Use Case |
Manual | Hand-cranked | Small flanges in tight spots |
Pneumatic | Air | Mid-sized flanges in plant settings |
Hydraulic | Hydraulic pump | Large-diameter pipeline systems |
Internal-Mount vs. External-Mount Machines
- Internal-Mount Flange Facers clamp inside the pipe bore and are ideal for compact spaces and flange diameters from 2” to 40”.
- External-Mount Flange Facers mount around the flange’s outer rim and offer a broader facing range, making them suitable for reactors, boilers, and heat exchangers.
Core Features of Petracarbon’s Flange Facers
At Petracarbon, flange facers are engineered with high-precision components to ensure repeatable results in the most demanding environments.
Adjustable Cutting Speeds for Multi-Material Versatility
Operators can fine-tune speed settings depending on material hardness:
- Carbon Steel: Higher speeds for efficient material removal
- Stainless Steel & Duplex: Slower speeds with carbide inserts to preserve surface integrity
Precision Feed Systems for Uniform Surface Finish
Our cutting head design enables:
- Consistent spiral finishes per ASME and EN gasket surface specs
- Controlled feed for grooves, serrations, or flat finishes depending on gasket type
Related Tooling: Hydraulic Torque Wrenches
Integration with Other Critical Maintenance Tools
Using Flange Facers Alongside Hydraulic Torque Wrenches
After facing a flange, proper bolt preload is critical. Our hydraulic torque wrenches apply even torque to ensure a uniform seal and prevent distortion of the freshly machined surface.
When Nut Splitters and Flange Spreaders Are Needed
Before flange facing, nut splitters and flange spreader tools safely remove seized fasteners and separate flanges-eliminating damage that could affect the refacing process.
Related Read: Flange Spreader Tools: Ensuring Safe and Efficient Flange Separation
Ensuring Fixture Stability and Pin Contact During Facing
Lessons from ICT Fixtures Using 3070/Teradyne Systems
The same engineering philosophy behind stable PCB test fixtures-like those used in 3070 and Teradyne automated test equipment-applies to flange machining. Just as spring contact pins must land with perfect alignment for accurate electrical testing, a flange facer must maintain concentricity and rigidity for a uniform cut.
Fixture Design Principles for Reliable Facing
- Dual clamping for vibration control
- Reinforced base plates (similar to ATE test fixture frames)
- Low-friction guides for linear feed systems
Industrial Applications of Flange Facers
Oil & Gas Facilities
Used during shutdowns and emergency maintenance to recondition flanges on high-pressure pipelines, heat exchangers, and valve bodies-without pipe removal.
Petrochemical Plants and Power Generation
Essential in turbine systems, reactors, and condensate loops where temperature cycles and chemical corrosion distort sealing surfaces over time.
Offshore and Marine
Compact, portable flange facers excel on ships, drilling platforms, and FPSOs where space is limited and crane access is unavailable.
Maintenance, Safety, and Calibration Best Practices
Blade Wear, Lubrication & Calibration
- Change inserts after 20–30 flange cuts
- Lubricate feed screws and shafts before each job
- Calibrate feed rate to achieve correct spiral finish depth (e.g. 125–250 AARH)
Operator Safety Measures
- Always depressurize systems before disassembly
- Secure flange position with blocks or straps
- Wear face shields and flame-retardant clothing in hydrocarbon environments
Choosing the Right Flange Facer for Your Operation
Factor | Consideration |
Diameter Range | From 2” to over 72” |
Mounting Type | Internal vs. external |
Power Requirements | Manual, pneumatic, or hydraulic |
Site Conditions | Hazardous, offshore, or confined-space rated |
When to Rent vs. Buy?
- Buy for long-term facility operations
- Rent for short-term shutdowns or emergency repairs
Contact Petracarbon to discuss project scope and choose the right equipment.
Refacing with Precision and Confidence
Flange facing is more than surface repair-it’s an essential part of ensuring joint integrity in systems that can’t afford to fail. With Petracarbon’s precision-engineered flange facers, industries across Southeast Asia and beyond can restore sealing surfaces quickly, safely, and reliably.
Whether you’re working offshore, in a petrochemical plant, or on a power grid, trust Petracarbon’s tooling solutions to keep your systems aligned, sealed, and leak-free-every time.
Explore more at Petracarbon.com