Heavy-duty bolting is essential in industries such as oil and gas, power generation, and construction, where secure and precise fastening is critical for safety and efficiency. Whether you’re working with pipelines, pressure vessels, or structural assemblies, using the right tools and techniques can prevent equipment failures, leaks, and costly downtime.
In this article, we will explore the importance of precision in heavy-duty bolting and the key tools that ensure safe and efficient bolted joints, including hydraulic bolt tensioners, hydraulic torque wrenches, flange facing machines, flange spreader tools, and flange alignment tools.
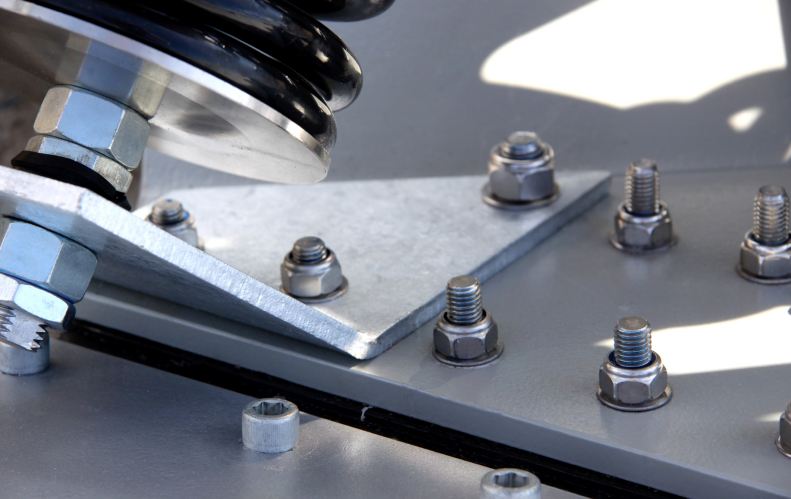
Understanding Heavy-Duty Bolting
Heavy-duty bolting involves securing high-strength bolts and nuts in critical applications where standard tightening methods are insufficient. It requires precise preload, sealing, and alignment to prevent structural failures.
Why Precision Matters? | Impact on Industrial Operations |
Prevents Leaks | Ensures tight, secure joints in high-pressure environments |
Avoids Equipment Damage | Reduces bolt fatigue, ensuring longevity |
Enhances Safety | Prevents accidents and system failures |
Saves Costs | Reduces unplanned maintenance and downtime |
Essential Tools for Safe and Precise Bolting
Hydraulic Bolt Tensioners – Even Load Distribution
Hydraulic bolt tensioners provide a controlled way to tighten bolts by applying direct axial force. Unlike traditional methods that rely on torque, these tools stretch the bolt evenly before the nut is secured, ensuring consistent preload.
Key Benefits:
- Ensures uniform bolt tension across all fasteners.
- Eliminates thread friction, reducing wear and tear.
- Speeds up the bolting process, improving efficiency.
- Enhances safety by minimizing the risk of over-tightening.
Common Applications: Pipelines, offshore platforms, and power plants.
Hydraulic Torque Wrenches – Precise Torque Application
Hydraulic torque wrenches are designed to apply a specific amount of torque to bolts, ensuring accurate and repeatable tightening. They are ideal for applications requiring controlled force, such as flange connections and structural assemblies.
- Provides precise torque settings for consistent tightening.
- Reduces the risk of bolt damage or failure.
- Suitable for confined spaces where large tools cannot be used.
Advantages of Using Hydraulic Torque Wrenches:
Common Applications: Flange bolting, structural assemblies, and industrial machinery.
Pro Tip: Using hydraulic torque wrenches can reduce manual labor and increase efficiency by up to 40%!
Flange Facing Machines – Smoother Sealing Surfaces
Flange facing machines are used to restore damaged or corroded flange faces, ensuring a smooth and even surface for sealing. In industries where high-pressure sealing is required, an uneven flange face can lead to leaks and gasket failures.
Why Use a Flange Facing Machine?
- Ensures a flat, smooth flange surface for better sealing.
- Helps prevent leaks by improving gasket contact.
- Available in portable versions for on-site repairs.
Common Applications: Oil refineries, petrochemical plants, and high-pressure piping systems.
Flange Spreader Tools – Safe and Efficient Flange Separation
Benefits of Flange Spreader Tools:
- Prevents damage to flanges and gaskets.
- Reduces the risk of worker injury by eliminating the need for manual prying.
- Works with a variety of flange sizes and materials.
Common Applications: Pipeline maintenance, chemical processing, and pressure vessel repairs.
Pro Tip: Using flange spreader tools can reduce flange separation time by 50% compared to manual methods.
Flange Alignment Tools – Correcting Misalignment Before Bolting
Flange alignment tools help ensure that two flanges are properly positioned before bolting, preventing stress on bolts and gaskets. Misalignment can lead to joint failure, leaks, and bolt fatigue, making proper alignment a crucial step in the bolting process.
Why Flange Alignment Tools Are Important:
- Ensures parallel flange faces for even gasket compression.
- Reduces installation time and simplifies alignment.
- Prevents joint failure by minimizing bolt stress.
Common Applications: Industrial piping, shipbuilding, and heavy equipment maintenance.
Pro Tip: Misaligned flanges are responsible for 80% of bolted joint failures – using the right alignment tools prevents costly rework!
Best Practices for Safe and Efficient Bolting
- Choose the Right Tool for the Job: Select hydraulic bolt tensioners for even preload and hydraulic torque wrenches for precise torque control.
- Inspect and Prepare Flanges: Check for damage and use a flange facing machine if necessary to ensure a smooth sealing surface.
- Follow the Correct Tightening Sequence: Always follow manufacturer-recommended torque sequences to ensure even load distribution.
- Monitor and Maintain Bolted Joints: Regular inspections can help detect loose bolts or alignment issues before they become critical problems.
Conclusion: Building a High-Performance Wireless Network
Achieving precision and safety in heavy-duty bolting is crucial for industrial applications where reliable fastening is essential. By using specialized tools such as hydraulic bolt tensioners, hydraulic torque wrenches, flange facing machines, flange spreader tools, and flange alignment tools, professionals can ensure secure, leak-free, and long-lasting bolted joints.
For high-quality bolting solutions and expert guidance, visit Petracarbon.
If you need assistance choosing the right bolting tools for your application,
contact Petracarbon today.
Stay precise, stay safe!